top of page
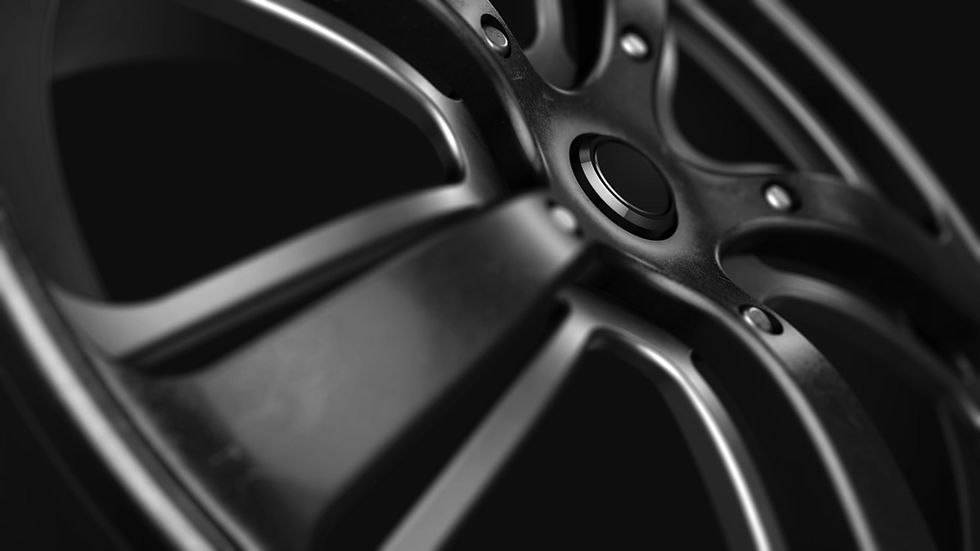
REVERSE ENGINEERING
We are Pioneer in providing Reverse Engineering Services to Multiple Industries Like Automotive, Electronics , Medical and more !
Get in touch with Us to Discuss your requirement.

Photogrammetry
photogrammetry takes many pictures of an object from different perspectives. Later, specialized software analyzes all these photos, looking for characteristic points of the objects and identifying where these points are in each image. Through this analysis a point cloud is generated, which can later be converted into a 3D object.
Advantage of using photogrammetry over 3D scanning is price and accessibility. A camera and photogrammetry software are usually less expensive, and much easier to transport! You might already have a camera as well (often a mobile phone camera will work).
Another important advantage of photogrammetry is its ability to reproduce an object in full color and texture. Though some 3D scanners can produce this as well, photogrammetry is the method to use when you’re looking for realism.
Lastly, an interesting advantage is that photogrammetry can work at many scales and sizes. You can model the tip of a finger or a whole mountain range. Other 3D scanners are limited to a particular sized object.
Advantage of using photogrammetry over 3D scanning is price and accessibility. A camera and photogrammetry software are usually less expensive, and much easier to transport! You might already have a camera as well (often a mobile phone camera will work).
Another important advantage of photogrammetry is its ability to reproduce an object in full color and texture. Though some 3D scanners can produce this as well, photogrammetry is the method to use when you’re looking for realism.
Lastly, an interesting advantage is that photogrammetry can work at many scales and sizes. You can model the tip of a finger or a whole mountain range. Other 3D scanners are limited to a particular sized object.

WHITE LIGHT SCANNER
Laser based 3D scanners use a process called trigonometric triangulation to accurately capture a 3D shape as millions of
points. Laser scanners work by projecting a laser line or multiple lines onto an object and then capturing its reflection
with a single sensor or multiple sensors. The sensors are located at a known distance from the laser's source. Accurate
point measurements can then be made by calculating the reflection angle of the laser light.
Benefits of 3D Laser Scanners
Able to scan tough surfaces, such as shiny or dark finishes
Less sensitive to changing light conditions and ambient light
Often more portable
Simpler design – easier to use and lower cost
points. Laser scanners work by projecting a laser line or multiple lines onto an object and then capturing its reflection
with a single sensor or multiple sensors. The sensors are located at a known distance from the laser's source. Accurate
point measurements can then be made by calculating the reflection angle of the laser light.
Benefits of 3D Laser Scanners
Able to scan tough surfaces, such as shiny or dark finishes
Less sensitive to changing light conditions and ambient light
Often more portable
Simpler design – easier to use and lower cost
bottom of page